How to calculate the heat duty for heat Exchangers ?
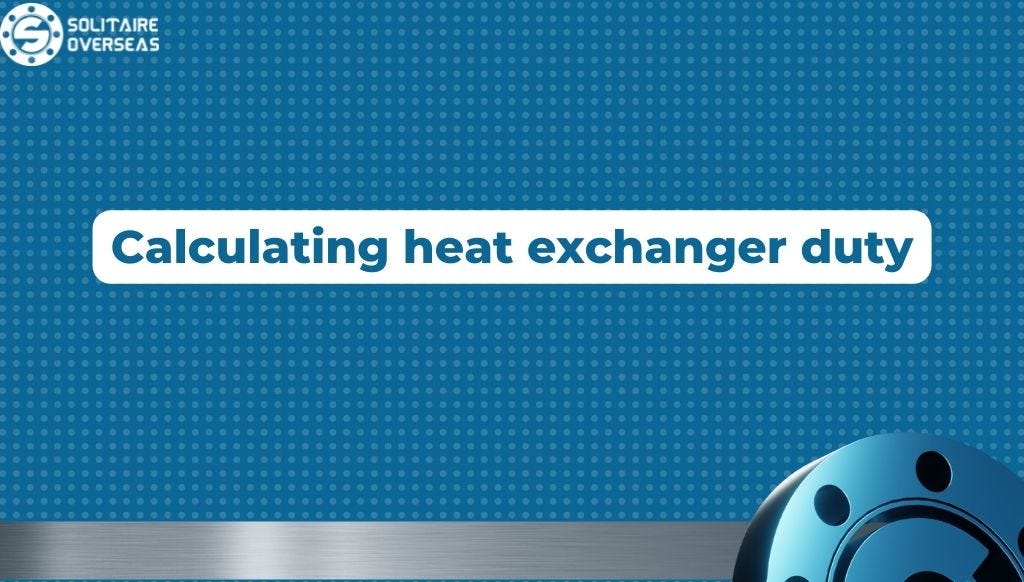
In order to understand exactly what we are calculating, let’s define the term “Heat duty.”. It is the amount of heat required to transfer from a hot side to a cold side over a period of time. The calculation is important to all engineers and one of the most common calculations you’ll need to know in your career if you’re a process engineer. There are two ways to calculate heat duty.
Speaking of Heat Exchangers, specialised boiler tubes are utilised in proper functioning of such exchangers. SA179tube.com Is one leading Manufacturer, Supplier & Stockist Of Boiler Tubes A210 Tubes And SA 210 Tubes.
Fluids that are suitable for sensible heat transfer, that is, fluids that do not undergo phase changes.Latent heat transfer, on the other hand, occurs when a fluid undergoes a phase change. i.e. condenses.
How to calculate the heat duty for heat exchangers?
A210 Tubes And SA 210 Tubes Play Important Role In Heat Exchanger. To begin understanding exactly what we are calculating, let’s define the term “Heat duty”. Heat duty can be defined as the amount of heat that has to be transferred from a hot to a cold side over the course of a unit of time.
A process engineer needs to know this calculation because it’s one of the most common ones. There are normally two ways to calculate heat duty.
Fluids that can be used for sensible heat transfer, meaning they do not undergo phase change.
In order to solve a thermal problem, we need to know several parameters. From there, further data can be determined.
The six most important parameters include:
- The amount of heat to be transferred (heat load)
- The inlet and outlet temperatures on the primary and secondary sides
- The maximum allowable pressure drop on the primary and secondary sides
- The maximum operating temperature
- The maximum operating pressure
- The flowrate on the primary and secondary sides
The heat load can be calculated if the flow rate, specific heat and temperature difference on one side are known.
Calculation method
The heat load of a heat exchanger can be derived from the following two formulas:
1. Heat load, Theta and LMTD calculation

Where:
P = heat load (btu/h)
m = mass flow rate (lb/h)
cp = specific heat (btu/lb °F)
δt = temperature difference between inlet and outlet on one side (°F)
k = heat transfer coefficient (btu/ft2 h °F)
A = heat transfer area (ft2)
LMTD = log mean temperature difference

T1 = Inlet temperature – hot side
T2 = Outlet temperature – hot side
T3 = Inlet temperature – cold side
T4 = Outlet temperature – cold side
LMTD can be calculated by using the following formula, where ∆T1 = T1–T4 and ∆T2 = T2–T3

2. Heat transfer coefficient and design margin
The total overall heat transfer coefficient k is defined as:

α1 = The heat transfer coefficient between the warm medium and the heat transfer surface (btu/ft2 h °F)
α2 = The heat transfer coefficient between the heat transfer surface and the cold medium (btu/ft2 h °F)
δ = The thickness of the heat transfer surface (ft)
Rf = The fouling factor (ft2 h °F/btu)
λ = The thermal conductivity of the material separating the medias (btu/ft h °F)
kc = Clean heat transfer coefficient (Rf=0) (btu/ft2 h °F)
k = Design heat transfer coefficient (btu/ft2 h °F)
M = Design Margin (%)
Combination of these two formulas gives: M = kc · Rf
i.e the higher kc value, the lower Rf-value to achieve the same design margin.
SA179tubes.com is a leading supplier, stockist, manufacturer & exporter of A210 Tubes & SA 210 Tubes. Get in touch with us for the best rates & availability.
Heat exchangers transfer heat from one fluid to another. In a heat exchanger, one fluid flows through a tube and another fluid flows by on the outside.
To understand what we are calculating, let’s define “Heat duty”. Over a period of time, it is the amount of heat transferred from a hot side to a cold side.
A sensible heat transfer fluid is one that does not undergo phase changes during heat transfer.
During heat transfer, a sensible fluid does not undergo phase changes.
There are normally two ways to calculate heat duty.
Latent heat transfer, on the other hand, occurs when a fluid undergoes a phase change.