A weld neck flange, also known as a tapered hub flange or high-hub flange, is designed to transfer stress to the pipes, reducing high-stress concentration at the base. There are two designs of weld neck flanges: the first type is used with pipes, while the second, longer type is used with process plants rather than pipes. This flange features a round fitting that extends beyond the rim.
These weld neck flanges are typically made from forgings and are welded to the pipes. The rim has multiple holes drilled into it, allowing the flange to be connected to a bolted flange. This design offers a superior structural advantage due to its robust and efficient construction.
A long weld neck (LWN) flange resembles a typical welding neck flange but is elongated. It is commonly used as a nozzle for columns or barrels. There are two main types: the Equal LWN Barrel and the LWN Heavy Barrel, both of which have thick walls and distinct shapes to accommodate different applications.
A reducing weld neck flange, also known as a reducing welding neck flange, features a neck with a reducing diameter, allowing it to be welded to a smaller diameter pipe. This design makes it useful for connecting pipes of different sizes while maintaining structural integrity.
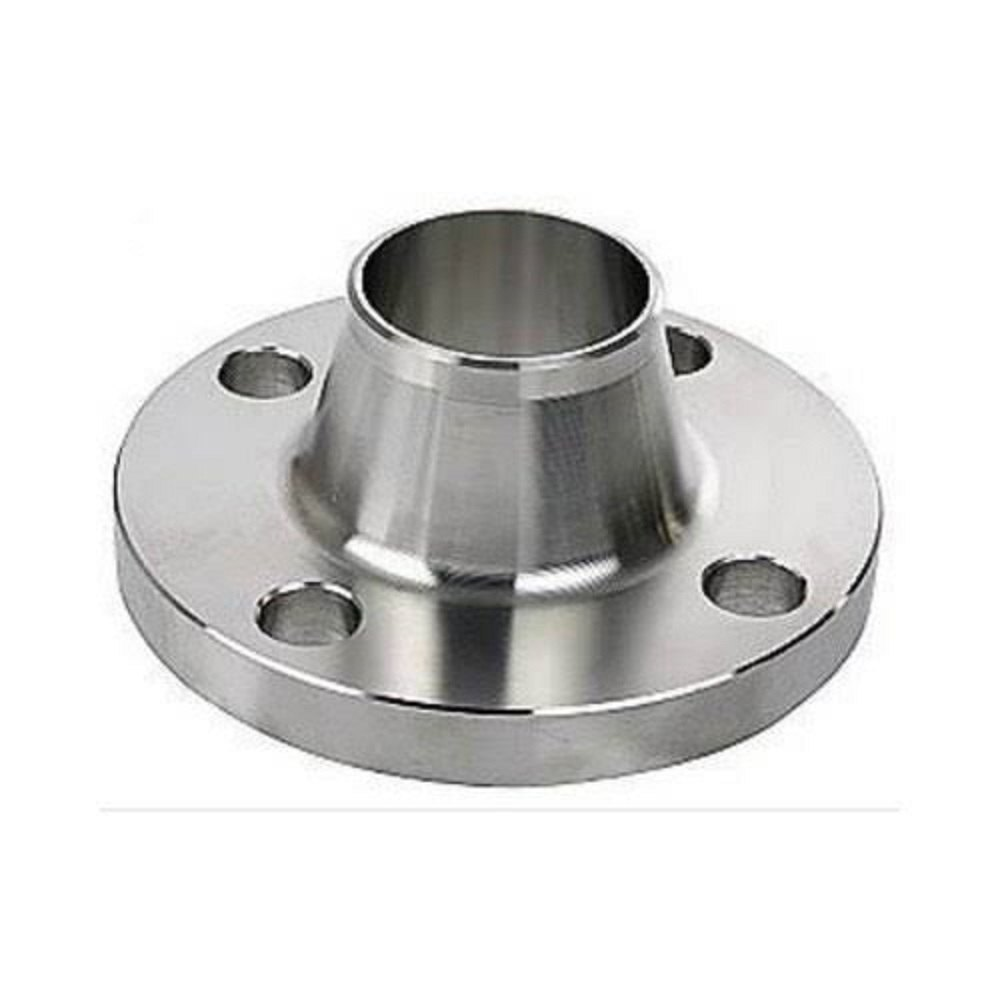
Long Weld Neck Flanges are a type of high-hub flange designed to transfer stress to the pipe, reducing stress concentration at the base of the flange. This design ensures a more even distribution of stress, enhancing the durability and reliability of the connection.
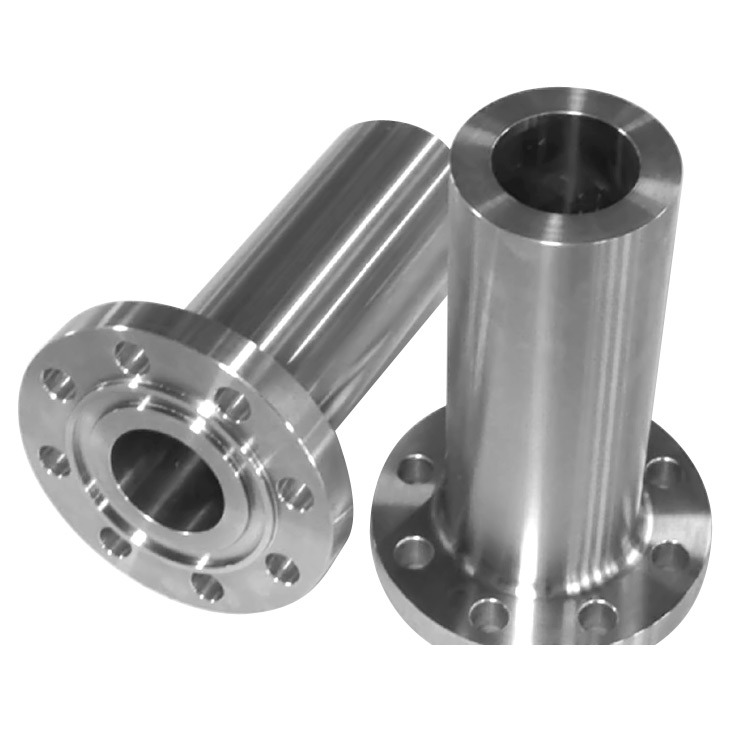
Materials of WN Flanges
Welding neck flanges come in a variety of materials, all adhering to stringent ASTM or ASME standards. The choice of material depends on the specific requirements and environmental conditions they will encounter.
Carbon Alloy: Carbon alloy is a popular choice due to its resistance to extreme temperatures. It is commonly available in ASTM A181 and ASTM A105 grades. These flanges are categorized into ASME B16.47 'A' Series and 'B' Series, tailored to meet diverse industry needs.
Stainless Steel: Stainless steel welding neck flanges are crafted from materials like ASTM A182, F304, 316L, 347H, and 310S, conforming to ASME B16.5 standards. They often feature a duplex steel finish, with UNS S31803 duplex steel also widely used.
Nickel Alloy: For specialized applications, nickel alloy welding neck flanges are manufactured from materials such as Inconel 600 and 625, Hastelloy C22, C276, and others. These alloys offer superior corrosion resistance and high-temperature performance.
Each material choice ensures that welding neck flanges maintain robustness and reliability in demanding industrial environments, catering to varied piping needs with durability and performance in mind.
Weld Neck Flange Dimension
Below we list some sizes of weld neck flanges (Class 150) under ASME B16.5 (1/2” to 24”).
Size in Inch | Size in mm | Outer Diameter | Flange Thickness | Hub OD | Weld Neck OD | Welding Neck Length | Bore | RF Diameter | RF Height | PCD | Weld Face |
---|---|---|---|---|---|---|---|---|---|---|---|
A | B | C | D | E | F | G | H | I | J | ||
1/2 | 15 | 90 | 9.6 | 30 | 21.3 | 46 | Welding Neck bore is derived from the pipe schedule | 34.9 | 2 | 60.3 | 1.6 |
3/4 | 20 | 100 | 11.2 | 38 | 26.7 | 51 | 42.9 | 2 | 69.9 | 1.6 | |
1 | 25 | 110 | 12.7 | 49 | 33.4 | 54 | 50.8 | 2 | 79.4 | 1.6 | |
1 1/4 | 32 | 115 | 14.3 | 59 | 42.2 | 56 | 63.5 | 2 | 88.9 | 1.6 | |
1 1/2 | 40 | 125 | 15.9 | 65 | 48.3 | 60 | 73 | 2 | 98.4 | 1.6 | |
2 | 50 | 150 | 17.5 | 78 | 60.3 | 62 | 92.1 | 2 | 120.7 | 1.6 | |
2 1/2 | 65 | 180 | 20.7 | 90 | 73 | 68 | 104.8 | 2 | 139.7 | 1.6 | |
3 | 80 | 190 | 22.3 | 108 | 88.9 | 68 | 127 | 2 | 152.4 | 1.6 | |
3 1/2 | 90 | 215 | 22.3 | 122 | 101.6 | 70 | 139.7 | 2 | 177.8 | 1.6 | |
4 | 100 | 230 | 22.3 | 135 | 114.3 | 75 | 157.2 | 2 | 190.5 | 1.6 | |
5 | 125 | 255 | 22.3 | 164 | 141.3 | 87 | 185.7 | 2 | 215.9 | 1.6 | |
6 | 150 | 280 | 23.9 | 192 | 168.3 | 87 | 215.9 | 2 | 241.3 | 1.6 | |
8 | 200 | 345 | 27 | 246 | 219.1 | 100 | 269.9 | 2 | 298.5 | 1.6 | |
10 | 250 | 405 | 28.6 | 305 | 273 | 100 | 323.8 | 2 | 362 | 1.6 | |
12 | 300 | 485 | 30.2 | 365 | 323.8 | 113 | 381 | 2 | 431.8 | 1.6 | |
14 | 350 | 535 | 33.4 | 400 | 355.6 | 125 | 412.8 | 2 | 476.3 | 1.6 | |
16 | 400 | 595 | 35 | 457 | 406.4 | 125 | 469.9 | 2 | 539.8 | 1.6 | |
18 | 450 | 635 | 38.1 | 505 | 457.2 | 138 | 533.4 | 2 | 577.9 | 1.6 | |
20 | 500 | 700 | 41.3 | 559 | 508 | 143 | 584.2 | 2 | 635 | 1.6 | |
24 | 600 | 815 | 46.1 | 663 | 610 | 151 | 692.2 | 2 | 749.3 | 1.6 |
Specifications of Weld Neck Flanges
Weld neck flanges are crucial components in piping systems, designed to withstand high pressure and ensure reliable sealing. Here are the essential specifications and standards for weld neck flanges:
- Common Outer Diameters: 1/2”, 2”, 3”, 4”, 6”, 8”, 10”, 12” to 24”
- Special Made Outer Diameters: Up to 60”
- Class Range: Class 150, 300, 400, 600, 900, 1500, 2500 (# or LB); PN 2.5 to PN 250
- Flange Face Type: RF (Raised Face), RTJ (Ring Type Joint)
Standards for Weld Neck Flanges:
- ASTM A105:Carbon steel welding neck flanges
- ASTM A182: Alloy and stainless welding neck flange (Alloy includes F11, F22; stainless includes F304/F304L, F316/F316L)
- ASME B16.5: Standard for pipe flanges and flanged fittings
- ASME B16.47: Large diameter steel flanges (NPS 26 through NPS 60)
- BS 3293: Specification for carbon steel pipe flanges (over 24 inches nominal size) li>DIN Standards: DIN 2630 PN 1 and PN 2.5, 2631 PN 6, 2632 PN 10, 2634 PN 16, 2634 PN 25, 2635 PN 40
Before ordering weld neck flanges, it’s crucial for companies to confirm:
- Material standard (e.g., ASTM A105, ASTM A182)
- Outer diameter (size ranging from 1/2” to 60”)
- Pressure class (Class 150 to 2500 or PN 2.5 to PN 250)
- Face type (RF or RTJ) li>Thickness schedule (e.g., Schedule 40)
Example Standard Description: "Flange, 10” Weld Neck, Class 150, RF, Schedule 40, ASTM A105 ASME B 16.5."
These specifications ensure weld neck flanges meet industry standards and are suitable for a wide range of applications in various sectors including oil and gas, chemical processing, and power generation.
Weld Neck Flange Class 150 and 300 Dimensions and Weight
6” Weld Neck Flange Class 150 and 300 Dimensions and Weight
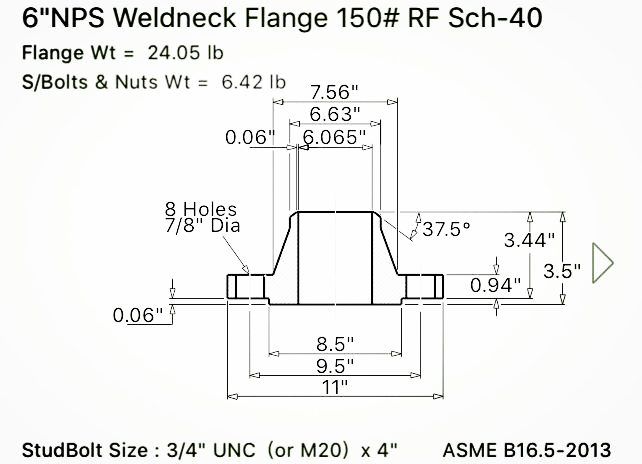
Class 300 Welding Neck Flange in 6 inch (Raised Face) Weight 20.13 KG
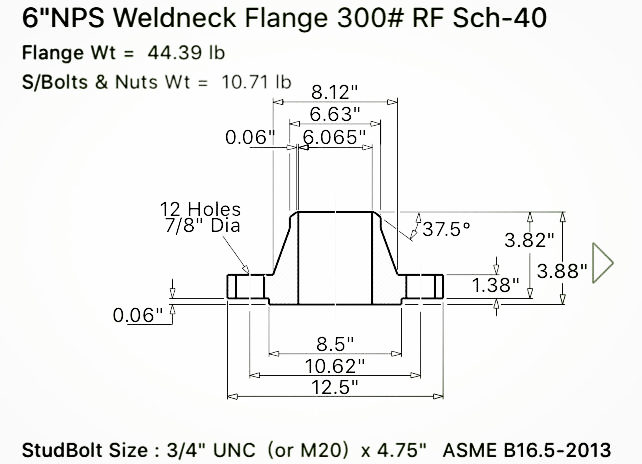
Welding Neck Flange Class 150 in 4 inch (RF) Weight 7.12 KG
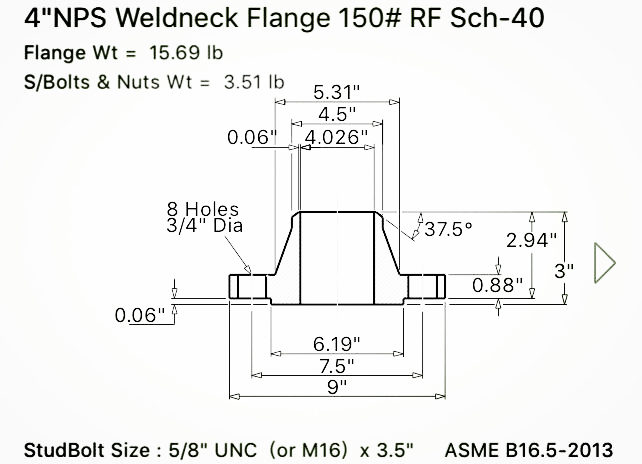
Supply and Exporter of Weld Neck Flange
Taiwan, Mexico, Iran, Namibia, Afghanistan, Netherlands, Nepal, Ireland, Libya, Morocco, Iran, Switzerland, Finland, Slovakia, Pakistan, Australia, Serbia, Angola, China, Philippines, Czech Republic, Belgium, Estonia, Costa Rica, Croatia, Sweden, Venezuela, Colombia, India, Belarus, Jordan, Azerbaijan, Mongolia, Vietnam, Ghana, Iraq, Algeria, Puerto Rico, New Zealand, Singapore, Indonesia, Ukraine, Israel, Mexico, Hong Kong, Bhutan, Germany, Brazil, Plan, Yemen, Malasiya, USA, Cambodia, Laos, Uganda, Tanzania, Sudan, Democratic Republic of Congo, zambia, Ethiopia, Brunei, Madagascar, Niger, Mali, Bangladesh, Bolivia, United States, Ecuador, Lebanon, Italy, South Korea, Denmark, Norway, Sri Lanka, Zimbabwe, Japan, Yemen, Oman, Portugal, Lithuania, Canada, Macau, Bahrain, Austria, Bulgaria, Spain, Kenya, United Kingdom, United Arab Emirates, Kazakhstan, Egypt, Saudi Arabia, Gambia, Argentina, Romania, Tibet, France, Chile, Gabon, South Africa, Trinidad & Tobago,Tunisia, Turkey, Nigeria, Peru, Russia, Chile, Nigeria, Hungary, Qatar, Greece, Malaysia, Kuwait, Poland, Thailand, Poland,Germany, Belgium, Italy, Turkey, Denmark and UK.
FAQ
A weld neck flange is utilized in applications where severe conditions are present. These include high pressure, wide temperature and pressure fluctuations, volatile and hazardous fluids, and sub-zero temperatures.
A welded flange, specifically a weld neck flange, features a long tapered hub that smoothly transitions to the pipe or fitting it connects to. It's joined by butt-welding, where the end of the pipe is inserted into the flange and welded around its circumference. This method ensures a robust and leak-proof connection.
Three common types of flanges are:
- Weld Neck Flange: Known for its long tapered hub, this type of flange is butt-welded to the pipe. It's suitable for high-pressure applications due to its reinforcement and smooth transition.
- Slip-on Flange: These flanges slip over the pipe and are then welded in place. They are easier to align than weld neck flanges and are commonly used in low-pressure applications.
- Socket Weld Flange: Similar to slip-on flanges, socket weld flanges are welded to the pipe. They feature a socket into which the pipe end fits before welding, providing good flow characteristics and are used in smaller pipe sizes and high-pressure applications.
Each type of flange offers distinct advantages depending on the application's requirements for pressure, temperature, ease of assembly, and welding considerations.